

High-performance Retrofit Panel System testing on 3D scanned building model by Highland Park Technologies.
Written by Teddy Slosberg, Image by Christian Borger.
Deep Energy Retrofits (DER) are becoming increasingly common as building owners strive to maintain their assets and lower energy costs. However, the retrofit niche is limited from an economic standpoint. The most significant barrier to most DER’s is cost escalation. It can be expensive to retrofit buildings, and in some cases, the cost of DER exceeds the price tag of new construction. Most structures are unique and present different challenges, so a DER requries a thorough analysis of the subject building by the architects and engineers to determine the specific requirement for repair and energy performance upgrade. In addition to the building’s physical aspects, past renovations, outdated systems, and general wear may require such a high level of renovation that building occupants are displaced. Replacing a gas boiler or oil tank, installing new wiring, and changing all the lighting can make a DER into an unaffordable luxury. Unpredictable conditions may limit the building owner’s desire to undertake the renovation, as the first costs required for the project end up being too high despite the long-term benefits.
”… Unpredictable conditions may limit the building owner’s desire to undertake the renovation, as the first costs required for the project end up being too high despite the long-term benefits… “
Understanding that the success of a DER depends on controlling costs, Highland Park Technologies (HPT), an affiliated R&D group of West Work, determined that the most-effective way to improve a building’s energy performance is to reduce the air leakage and increase the insulation of the building envelope. HPT is developing a mass-producible insulated panel system that can improve a building’s energy performance at a reasonable cost. The panel is meant to compete with cladding and insulated siding products.
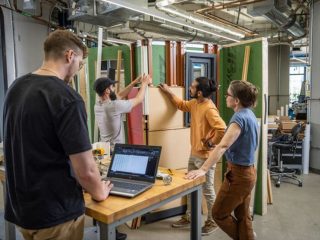

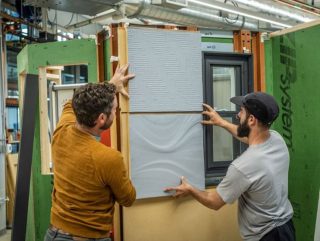

Highland Park Technologies Team testing material on 1:1 mock-up.
In Massachusetts, 54% of energy use comes from buildings. With improvements in the exterior envelope, Highland Park Technologies estimates a 50% reduction in energy use that will also significantly lower energy bills for the clients. Currently, the panel system targets triple-decker homes in the northeast, which comprise a considerable part of the existing housing stock (roughly 15,000), especially in the Boston Area. The panel is easily attached to the existing building sheathing, with standard shapes to handle corners and window openings. The panels are designed for architectural customization for a variety of patterns and colors. To date, the research and design for the HP Panels has been funded by grants from MassCEC, MassVentures, and the US Department of Energy. HPT was recently recognized as a Winner for Sustainable Construction Innovation at the 2023 BE+ Green Building Showcase. The team is among the residents at the Autodesk Technology Center in Boston’s Seaport District.